Our Services
We Offer a Range of Services Tailored to Your Needs
Our wide range of services is designed to meet all of your needs.
Control Applications
We use the latest technologies and products in the hydroelectric power plant solutions we produce. With the hardware and software we use, we design projects that will keep the plant’s security at a high level and meet all of the plant’s needs.
Scope of Automation Systems in Hydroelectric Power Plants (HPP):
-
Water level control,
-
Ensuring intake gate control,
-
Turbine monitoring and control,
-
Exciter and governor controls,
-
Synchronization of generators,
-
Control of HV, MV, and LV energy distribution and command systems,
-
Monitoring of protection relays and energy analyzers,
-
Monitoring of turbine temperatures,
-
Implementation of plant emergency shutdown scenarios,
-
Monitoring and controlling the plant via SCADA system and mimic control panel,
-
Turbine oil level information,
-
Open/close status of turbine cooling water valve,
-
Turbine governor oil level information,
-
Turbine governor oil pressure information,
-
Open/close control of turbine cooling water valve,
-
Open/close status of turbine inlet valve,
-
Open/close limit switch information for bypass,
-
Excitation, synchronization fault information,
-
Speed information,
-
Turbine governor start/stop control,
-
Turbine governor set value increase/decrease control,
-
Excitation system operation and fault information,
-
Command output.
Monitoring and Control of Internal Needs and Auxiliary Systems (110V DC, 24V DC, LV Systems):
-
Internal needs and auxiliary operation and fault information,
-
Status and fault information of LV circuit breakers,
-
Information from the air compressor (running, general fault, start/stop).
Synchronization Systems:
In the synchronization system, frequency and voltage adjustments are made for the turbines using synchronizer devices, ensuring that the units work in sync with each other or with the grid. The synchronization system can perform the synchronization operation either automatically or manually, depending on the request.
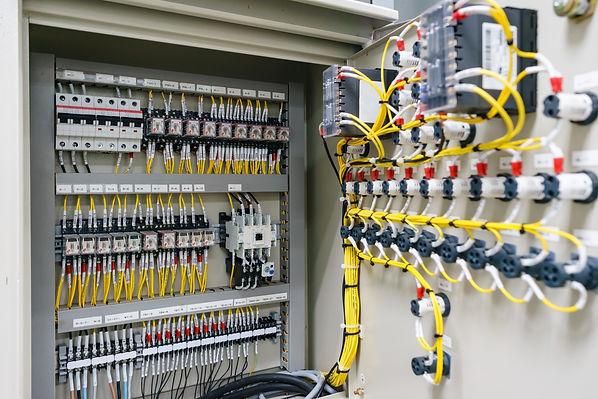

HPP-Hydroelectric Power Plant Automation
We use current technology and products in the hydroelectric power plant solutions we produce. With the hardware and software we use, we design the plant in a way that ensures its security and meets all its needs.
Scope of Automation Systems in Hydroelectric Power Plants (HPP):
-
Water level control,
-
Intake gate control,
-
Turbine monitoring and control,
-
Exciter and governor controls,
-
Synchronization of generators,
-
Control of HV, MV, and LV energy distribution and control systems,
-
Monitoring of protection relays and energy analyzers,
-
Control of turbine temperatures,
-
Implementation of emergency shutdown scenarios,
-
Monitoring and control via the SCADA system and mimic control panel,
-
Turbine oil level information,
-
Information on open/closed status of turbine cooling water valve,
-
Turbine governor oil level information,
-
Turbine governor oil pressure information,
-
Turbine cooling water valve open/close control,
-
Information on open/closed status of turbine inlet valve,
-
Information on bypass open/close limit switch,
-
Excitation and synchronization fault information,
-
Speed information,
-
Turbine governor start/stop control,
-
Turbine governor set value increase/decrease control,
-
Information on excitation system operation and faults,
-
Control outputs.
Monitoring and Control of Internal Needs and Auxiliary Systems (110V DC, 24V DC, LV Systems):
-
Internal needs and auxiliary operation and fault information,
-
Status and fault information of LV circuit breakers,
-
Information from the air compressor regarding operation, general faults, and start/stop.
Synchronization Systems: Synchronization systems use synchronizer devices to adjust the frequency and voltage of turbines, ensuring that units synchronize either with each other or with the grid. The synchronization system can perform the synchronization process either automatically or manually, depending on the preference.
PLC and SCADA System Design
• Manufacturing of MCC and PLC panels,
• Development of automation software,
• Design, manufacturing, testing, and installation of PLC and MCC panels,
• Automation systems testing, installation, and commissioning,
• In Energy SCADA Applications, monitoring of signals and electrical parameters (current, voltage, power, frequency, power factor, energy, harmonics, etc.) related to transformers, generators, UPS, LV distribution panels, MV distribution cells, and busbars,
• Establishing automation systems where electrical energy is generated, transmitted, distributed, and consumed, ensuring control and operation of the distribution and transmission system according to the optimal scenario, monitoring energy parameters, and tracking the system,
• Implementing RTU (Remote Terminal Unit) based systems to centralize widely dispersed energy systems under a single SCADA,
• Using fiber optic cables and RF modems, in addition to standard communication cables, depending on field conditions for communication,
• In generator systems operating in parallel with the grid, disconnecting excess loads within approximately 150 ms during network interruptions when the generator sets fail to fully cover the load,
• Establishing synchronization systems for diesel generators to operate in parallel with each other or with the grid. Automating systems equipped with Woodward products via PLC and delivering to the user via SCADA,
• Consultancy and engineering services in automation.


Cement Factory Automation
Modern cement processes and energy-efficient standards are achieved by minimizing human intervention, resulting in maximum production efficiency. This can only be accomplished through full automation of the entire system.
Correct Production can be achieved by:
-
Maximizing efficiency,
-
Easy product tracking,
-
Long-term low labor costs,
-
Process control, which can only be achieved through technology use and without human intervention.
In cement factories, as in all processes, the core principle is to correctly analyze and assess all operations, faults, and potential negative events in the system. Immediate interventions should be made based on these results, which can only be possible through automation systems.
Complete Turnkey Solutions We Offer: • O.G. (Medium Voltage) substation and circuit breakers,
• A.G. (Low Voltage) distribution panels,
• Compensation panels and harmonic filtering,
• MCC (Motor Control Center) Panels,
• PLC/RTU system installation engineering services,
• SCADA/DCS system installation and engineering services,
• Field instrumentation supply and calibration,
• Electrical installation and commissioning, etc.
With the rapid advancements in information technology, electrical, and electronics technology, significant progress has been made in the products used in automation and the electrical industry. In this technological race, we offer automation solutions in partnership with the industry leader Siemens.
We also provide turnkey automation solutions for process needs and offer local solutions. Some examples include: • Raw Material Preparation Unit (Crushing and Stocking), (Quarry),
• Pre-Homogenization Unit (Preblending),
• Raw Mill Unit (Proportioning, Blending, Grinding),
• Coal Mill Unit,
• Kiln Unit,
• Clinker Cooling and Transfer Unit (Preheater Tower),
• Cement Mill Unit (Kiln, Clinker Cooler, Finish Grinding),
• Packing Unit (Bagging and Shipping),
• Filter Shock Units,
• Trommel Dryer Unit,
• Mixing Plant,
• Ash Separator Unit,
• Electrofilter Unit,
• Flue Gas Automation,
• PLC Panels,
• SCADA Systems.
Additionally, for key machinery in cement plants, we also provide turnkey solutions such as: • Dosing Conveyors,
• Belt Scales,
• Weighing Units,
• Impact Plate Weighing Scales,
• Fully Automated Rotary Packaging Machines.
Plaster Factory Automation
We provide turnkey automation and electrical solutions for gypsum plants, and also offer the following localized solutions:
Localized Solutions: • Mobile Crushing Unit
• Factory Crushing and Screening Unit
• Calcination Unit
• Grinding and Separation Unit
• Storage Unit
• Dry Mixing Unit
• Perlite Expansion Unit
• Fine Calcite Feeding Unit
• Slaked Lime Feeding Unit
• Coarse Calcite Grinding and Feeding Unit
• Coarse Line Automatic Chemical Dosing Unit
• Fine Line Automatic Chemical Dosing Unit
• Compressed Air Unit
Benefits of the Systems We Establish for Our Clients: • Process continuity and the resulting savings in electricity, raw materials, labor, etc.
• Reduction in milling costs due to reduced waste and improved product quality
• Easy tracking of production stages
• Early detection and resolution of issues through data conversion to information
• Easy and accurate reporting of process data
Project Design and Development: The process begins by understanding the needs of the client, then creating quality, cost-effective solutions. These solutions are then detailed and designed, allowing potential issues to be addressed in the project phase.
Material Supply and Logistics Management: To provide the most efficient, cost-effective solutions with quality, material supply and logistics management are carried out using universal brands such as Siemens, Phoenix Contact, and Lapp Cable.
Panel Manufacturing and Projecting: For use in electrical and automation systems, we design and project the following panels in line with the location and environmental conditions of the project: • Main Distribution Panels
• Compensation Panels
• MCC Panels
• PLC/DCS Panels
• RIO/RTU Panels
• DDC Panels
Software Development and Integration: Our company uses SIEMENS STEP7, PCS7, WIN CC, TIA PORTAL, SIMOTION SCOUT software to provide seamless software solutions.
Supply and Calibration of Field Instrumentation: We supply and calibrate the field instruments necessary for the process, determining their placement and characteristics within the process.
Assembly and Commissioning: Our specialized team handles the assembly and commissioning of projects in the shortest time possible, ensuring that our clients can begin production as quickly as possible.

Wastewater Automation
Wastewater treatment can be achieved through chemical, physical, or biological methods:
-
Chemical Treatment: After passing through the sedimentation tank, various chemicals are added in the mixing unit, which react with the pollutants in the water, causing them to settle.
-
Biological Treatment: Domestic or industrial wastewater is treated with the help of various bacteria, and the waste from packaged treatment is biologically decomposed.
-
Physical Treatment: Without using chemicals or bacteria, the physical removal of fats and large waste from wastewater is done through mechanical processes such as screens, grease scrapers, and similar devices.
We offer turnkey automation and electrical solutions for wastewater treatment plants, as well as the following localized solutions: • Screens (fine or coarse)
• Pre-settlement tank
• Chemical treatment
• Grinding and separation unit
• Biological treatment units
• Dry mixing unit
• Final settlement tank
• Disinfection unit
Benefits of the Systems We Implement for Our Customers: • Process continuity and resulting gains in electrical energy, raw materials, labor, etc.
• Reduction in waste and lower grinding costs due to increased product quality
• Easy traceability of production stages
• Ability to convert data into information, allowing for proactive problem-solving
• Accurate and easy process reporting
Project Design and Development
By understanding the customer's needs, we provide high-quality, cost-effective solutions, and the project details are outlined to address any potential issues in the early stages.
Material Supply and Logistics Management
To offer the most efficient and cost-effective solutions from a process perspective, we use universal brands such as Siemens, Phoenix Contact, and Lapp Cable for material supply and logistics management while ensuring quality.
Panel Manufacturing and Design
Panels used in electrical and automation systems include:
• Main distribution panels
• Compensation panels
• MCC panels
• PLC/DCS panels
• RIO/RTU panels
• DDC panels
All panels are designed to suit the location and environmental conditions of the project and are designed using the E-Plan software within our company.
Software Development and Integration
We provide seamless software solutions using Siemens STEP7, PCS7, WIN CC, TIA PORTAL, and SIMOTION SCOUT software.
Field Instrumentation Supply and Calibration
The determination and supply of field instruments' locations and specifications in the process are done by our company.
Installation and Commissioning
Our installation and commissioning team, consisting of experts in their respective fields, ensures the rapid and flawless installation and commissioning of projects, enabling customers to start production as soon as possible.


Drinking Water Automation
Drinking Water Treatment System Automation Savings:
-
Labor force
-
Vehicles
-
Chemicals
-
Time
-
Water
-
Electricity
For drinking water treatment plants to meet modern and energy-efficient standards, it is essential to integrate the entire process into an automation system.
Like all processes, the key principle in drinking water treatment plants involves correctly analyzing, evaluating, and responding to operational issues, faults, and potential negative events. This can only be effectively achieved through an automation system.
Our Complete Turnkey Solutions:
-
Medium Voltage (MV) Switchgear and Circuit Breakers
-
Low Voltage (LV) Distribution Panels
-
Compensation Panels and Harmonic Filtering
-
Motor Control Center (MCC) Panels
-
Piano Panels (Aker Panels)
-
PLC/RTU System Installation Engineering Services
-
SCADA/DCS System Installation and Engineering Services
-
Supply and Calibration of Field Instrumentation
-
Lighting Systems
-
Electrical Assembly and Commissioning, etc.
With the advancement of information, electrical, and electronic technologies, significant progress has been made in automation and electrical products used in the sector. In this technological race, we offer automation solutions in partnership with Siemens, a leader in the field. We provide both turnkey automation solutions and local solutions for drinking water treatment processes, including:
-
Inlet and Pre-Chlorination Units
-
Rapid Mixing Units
-
Slow Mixing Units
-
Sedimentation Tanks
-
Rapid Sand Filters
-
Chlorine Contact Tank and Clean Water Storage
-
Chemical Units
-
Chlorination Units
-
By-Pass Units
-
MCC (Motor Control) Panels
-
PLC Panels
-
SCADA Systems